Unlocking Precision with Cnc Tools Essential Specifications and Best Practices for Global Buyers
Now, considering today's manufacturing scenario, with precision being the hallmark of the industry and efficiency considered sacred, CNC tools have been winning the battle of industrial innovations. With global buyers seeking reliable solutions for maximizing their production capabilities, it is vital to master the minimum specifications and best practices concerning CNC tools. These advanced tools allow manufacturers to create complex designs with utmost precision while streamlining processes, minimizing waste, and enhancing productivity.
However, knowing many CNC tools in the market can be downright terrifying for purchasing staff striving for informed decisions. This blog will unravel the minimum specifications of CNC tools, therefore illuminating several factors for assessing a quality product. Next, they will delve into best practices for buyers to maximize their investments and ensure that they are equipped with the right CNC tool for their unique operational needs. Come and let us illuminate the precision that CNC tools promise in your manufacturing processes.
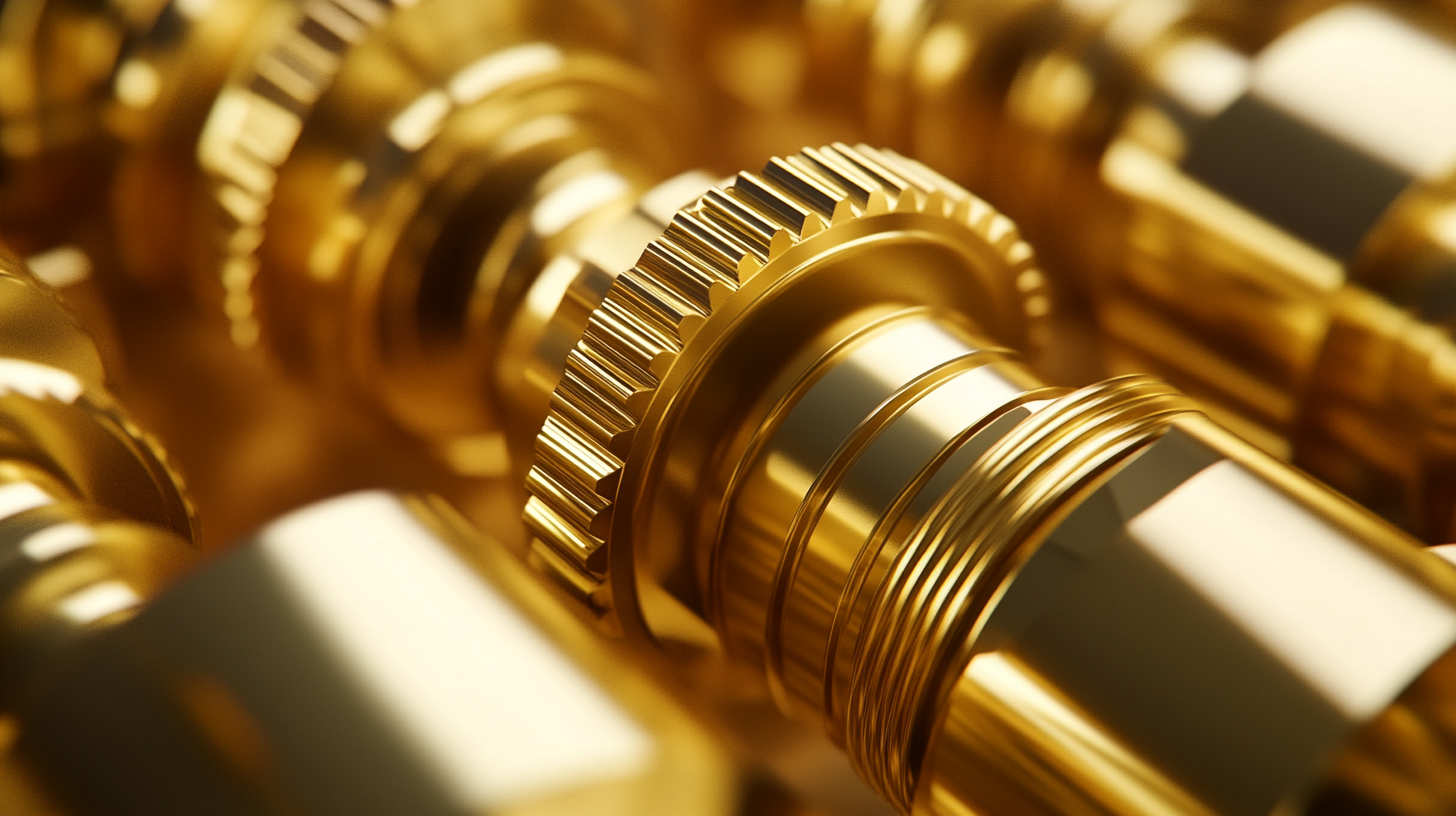
Key Specifications to Consider When Choosing CNC Tools for Precision Machining
Key specifications that affect performance and quality must be understood when selecting CNC tools for precision machining. MarketsandMarkets report states that by 2025, the CNC tools market is set to reach a height of $12.6 billion, indicating the immense demand for precision in manufacturing processes and recommending choosing CNC tools based on elaborated technical features. Material of the cutting tool is one of the most important specifications. Common tools include high-speed steel, carbide, and cermet. Each has individual advantages in terms of durability and heat resistance. Among these, carbide tools have the distinction of keeping their sharpness longest and acting most efficiently. Using different materials could significantly affect machining speed and quality, carbide tools speeding up production by as much as 25% against high-speed steel tools. Another factor highly considered has to do with tool geometry and design. These factors are known to greatly affect efficiency and precision in cutting. In reports, it has been stated that the number of flutes, rake angles and radius cutting edges are some important features used to cope with a specific task while machining. A research by Grand View Research states that around 15% gain in productivity can be achieved from CNC machines with optimized geometries. This shows the importance of paying close attention to these specifications when making selections. Also, accuracy is the measure of precision of CNC tools, which normally indicates the settings for tolerances and surface finish. Tools that have tolerance of ±0.005 inches are becoming increasingly favored with the concept that precision is again the keystone in quality machining, especially in aerospace and automotive. Specification standards not only improve production but also compliance with industry and customer demands forms an edge against competition in the market.
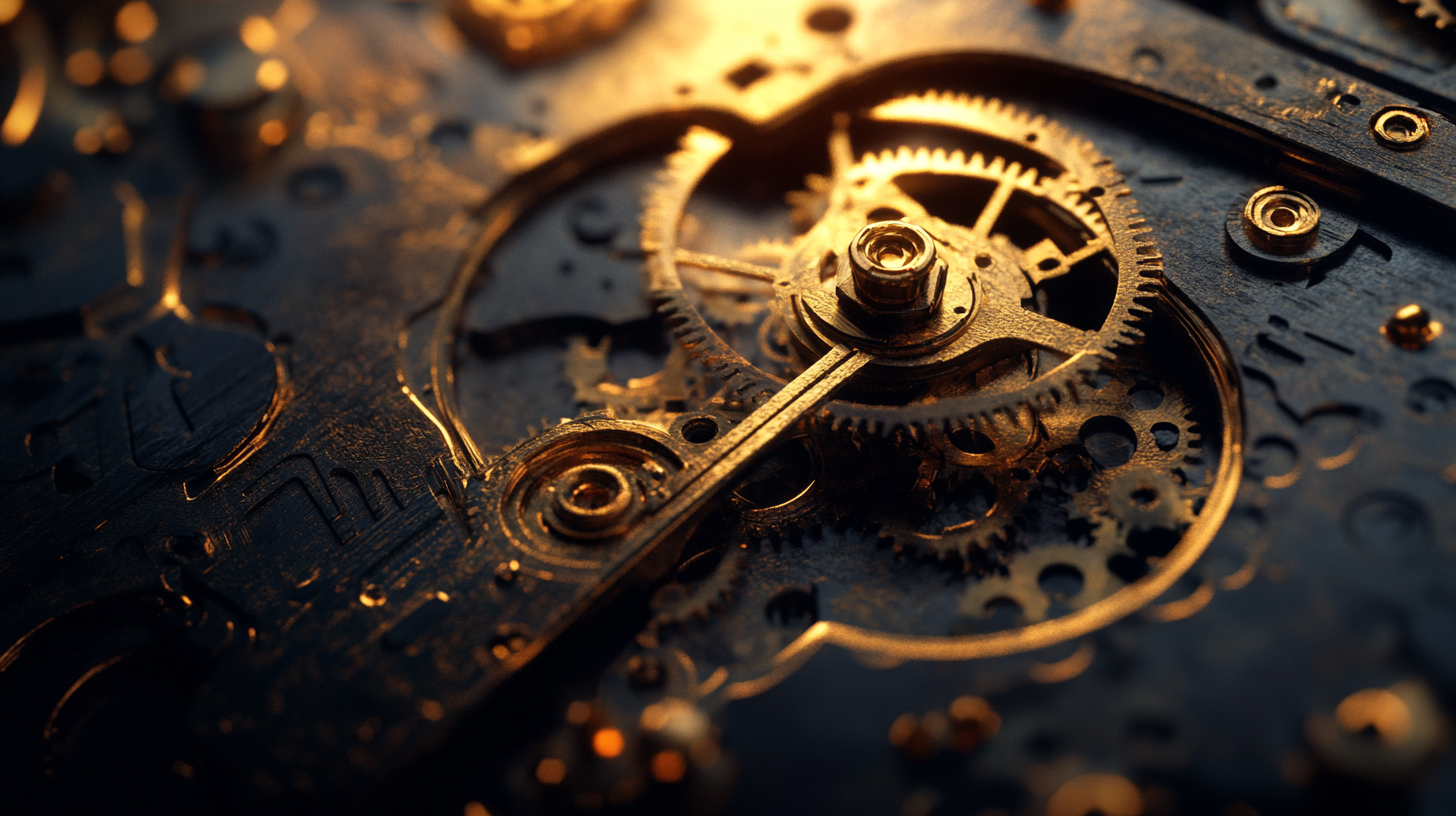
Understanding the Impact of Tool Materials on CNC Performance and Durability
In the emerging environment of CNC machining, the selection of tool materials is crucial for enhancing performance and durability. Global buyers who aim to improve their manufacturing processes also require an understanding of the relationship between tool materials and machining efficiency. The newest market trend shows an increasing scope for indexable milling tools, with the particular concentration on several blade materials and coatings, which cater to distinctive applications across industries.
Informed decision-making for prospective buyers concerning the selection of tools may warrant an understanding of several related factors up to the projections for the indexable milling tools market in 2032. For instance, in high-speed steel, carbide, and ceramic materials, all have differing advantages for wear resistance and heat tolerance factors, which play a role in the ultimate life of tooling. The layer may be coatings like TiN, TiAlN, or diamond-like carbon that enhance the performance properties by lowering friction, thus preventing the tool from wear, permitting a fine cut and better finish.
The other variable in a tool that can affect efficiency and economy is the number of cutting edges. Multi-edge tools save time on processes and enhance productivity, while those with single-edge designs may be best suited for specialized applications. As the market continues to grow and diversify, it becomes ever more important that buyers find their tool capabilities matched with specific machining needs, thereby enabling the realization of complete and full potential of CNC operations. With the exact materials and configurations, manufacturers will exploit unprecedented levels of precision and durability that can guarantee a sustained competitive edge in the global arena.
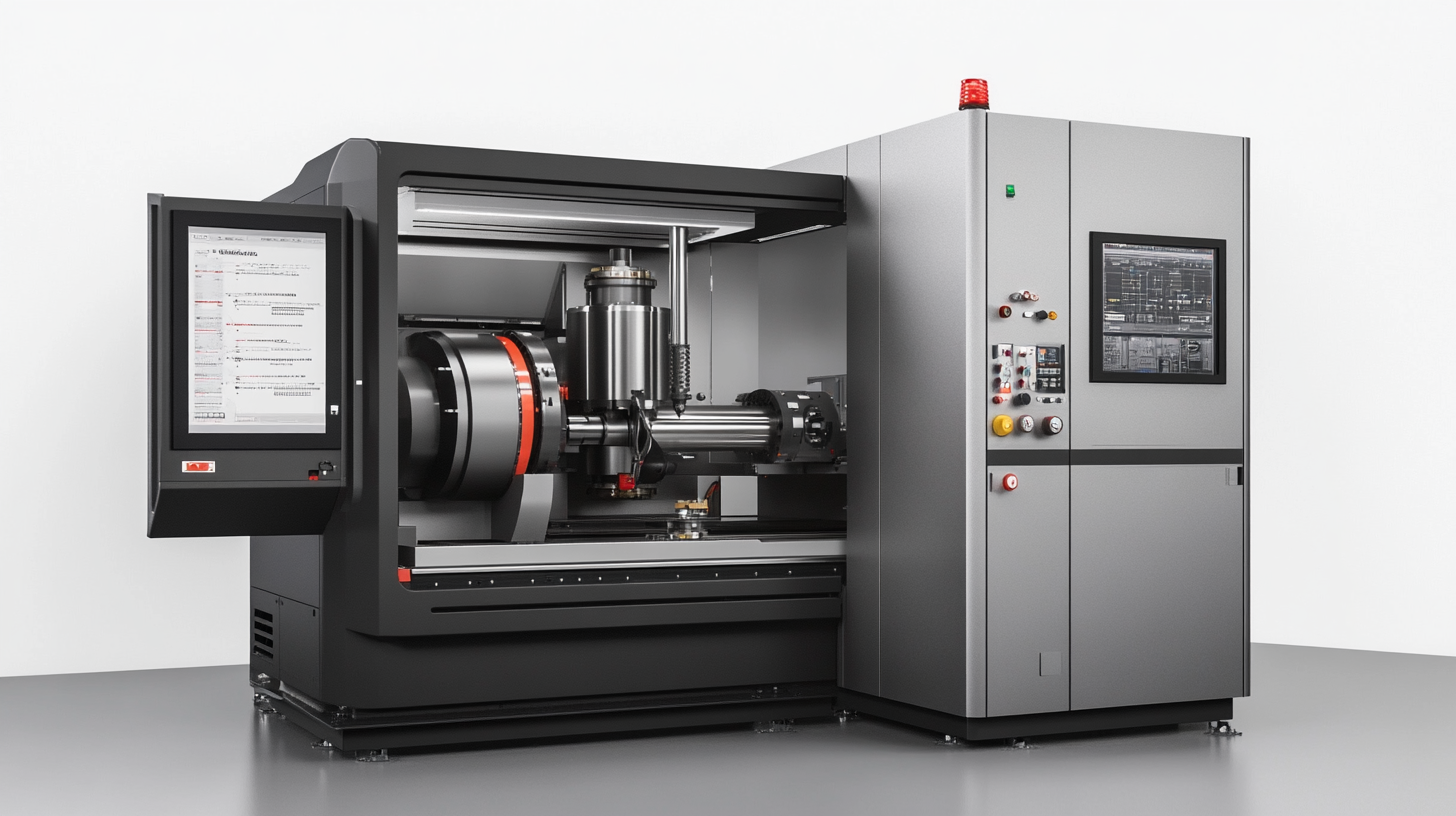
Best Practices for Maintaining CNC Tools to Ensure Longevity and Accuracy
To maintain CNC tools to ensure their long term life along with accuracy which is due to the aspect of digitalization and sustainability that the manufacturing industry is seeing, it is an important feature today. With more buyers around the world demanding precision while machining, well understanding of good practices in maintaining tools becomes imperative. Such schedules of regular maintenance of tools would include inspections, thorough cleaning, lubrication, and calibration of tools. All these would have a positive impact on extending the operational life of tools and enhancing their performance significantly.
Furthermore, recent advancements in CNC technology also avail manufacturing companies opportunities to embrace greenness. New CNC machinery can be purchased that meets the lifecycle standards of carbon footprint reduction: thus, these investments comply with industry regulations of production but encourage a sustainable way of work. This will allow companies to keep their competitive edge and environmental responsibility because they will keep investing in tools that minimize emissions and energy consumption.
AI and other digital technologies put on CNC operations improve the accuracy and efficiency of operations. Advanced monitoring systems will allow businesses to examine tool wear and prediction from the intervention to prevent as much downtime as possible and use as much productivity as possible. Staying true and adopting these best practices will ensure longevity for CNC tools and manufacturers as time can change.
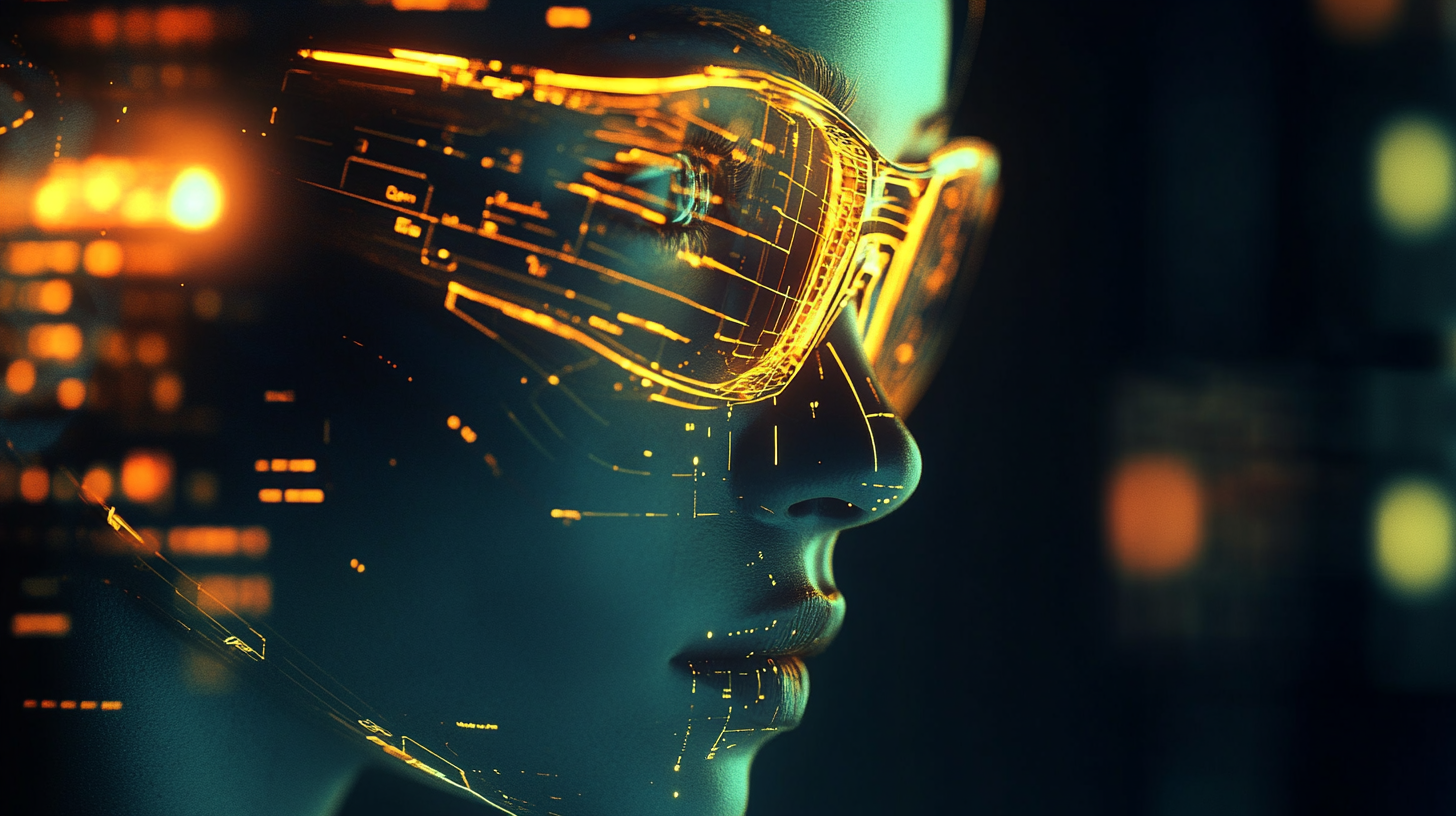
Navigating Global Supply Chains: Sourcing High-Quality CNC Tools
It has become an imperative to acquire pure and refined CNC tools, as precision and efficiency would the ideals of manufacturing operations in today's fast-paced global manufacturing environment. The demand for CNC tools emanating from industries such as automotive, aerospace, and general machinery, has generated projections for a huge potential future growth of the CNC tools market. For example, the global machine tool markets can exceed $97.1 billion by 2024 through a compound annual growth rate of 7.5% from 2025 to 2034. Such heavy growth reflects increasing reliance on advanced CNC technology to meet the modern complex and precision demands of manufacturing processes.
Global CNC tool supply chains possess one complicated-to-navigate maze. Expect high standards in sourcing, which would guarantee that the tools into the machines are most involved in precision machining. Supplier reliability, technology integration, and the extent of flexibility with regard to Industry 4.0 concepts are some of the elements to consider in making purchase decisions for the effective & efficient buyer. Companies can also serve to enhance their competitiveness through localized production capabilities while maintaining very global sourcing networks. Innovative CNC controllers and automation technologies combined with the efficiency of production can entirely streamline operations and propel any manufacturer into such a strong competitive position within a very dynamic market scenario.
Integrating Technology: CNC Tool Innovations Shaping the Future of Machining
The Taipei International Machine Tool Show had CNC technologies moving through a path of evolution, with great novelty and attraction to global buyers who see that innovative advancements are changing the landscape of machining. Companies such as Yida Precision Machinery show themselves as the epitome of sophistication. They were designed for smart and unconventional manufacturing solutions. As for new-generation CIM (Computer-Integrated Manufacturing) design, CNC systems are integrating with smart machinery. Tools, when backed by digital technologies, bring higher productivity and precision for various operating environments.
As aerospace industry has started painting pictures of where CNC applications come to the manufacturer, it therefore becomes clear that advanced manufacturing is well ahead of Industry 4.0. Even more, advancements in CNC technologies are turning a page towards standardized production excellence for high-value applications. The constant evolution of tools and technologies, displayed by other players such as the OIG-50 CNC internal grinder and the GMT-2000 five-axis combination turnmill, signifies an attitude of innovation toward configurations satisfying increasing as well as highly demanding markets.
It is, in an industry that makes tremendous strides in sustainable and intelligent equipment design, what actually seems merely practical and humane for harmonizing the degree of putting an edge to the environment vis-à-vis empowering machinist troops. The compression of CNC machinists has a promising feature of achieving its highest standards in digital knowledges just to tackle the complexities of the slowly turning mass-drive machinery-world and to meet the fancy of the world's clientele.