Revolutionizing Precision Cutting with Small Plasma Tables for Global Manufacturers
The manufacturing industry is witnessing a significant transformation with the introduction of advanced technologies that enhance precision and efficiency. According to a report by MarketsandMarkets, the global plasma cutting equipment market is projected to reach USD 7.8 billion by 2026, growing at a CAGR of 5.8%. This growth is fueled by the increasing adoption of automation in manufacturing processes and the rising demand for high-precision cutting applications across various sectors. Among these innovations, the Small Plasma Table stands out as a game-changer, enabling smaller manufacturers to access top-tier cutting capabilities that were once only available to larger operations.
Small Plasma Tables provide manufacturers with a flexible and cost-effective solution for precision cutting, allowing for a wide range of materials and intricate designs. As reported by ResearchAndMarkets, the demand for compact and efficient manufacturing solutions is on the rise, with small-scale manufacturers increasingly leveraging these technologies to remain competitive. By integrating Small Plasma Tables into their operations, businesses can optimize their production processes, reduce waste, and enhance overall productivity, ultimately revolutionizing the way precision cutting is approached in the global market.
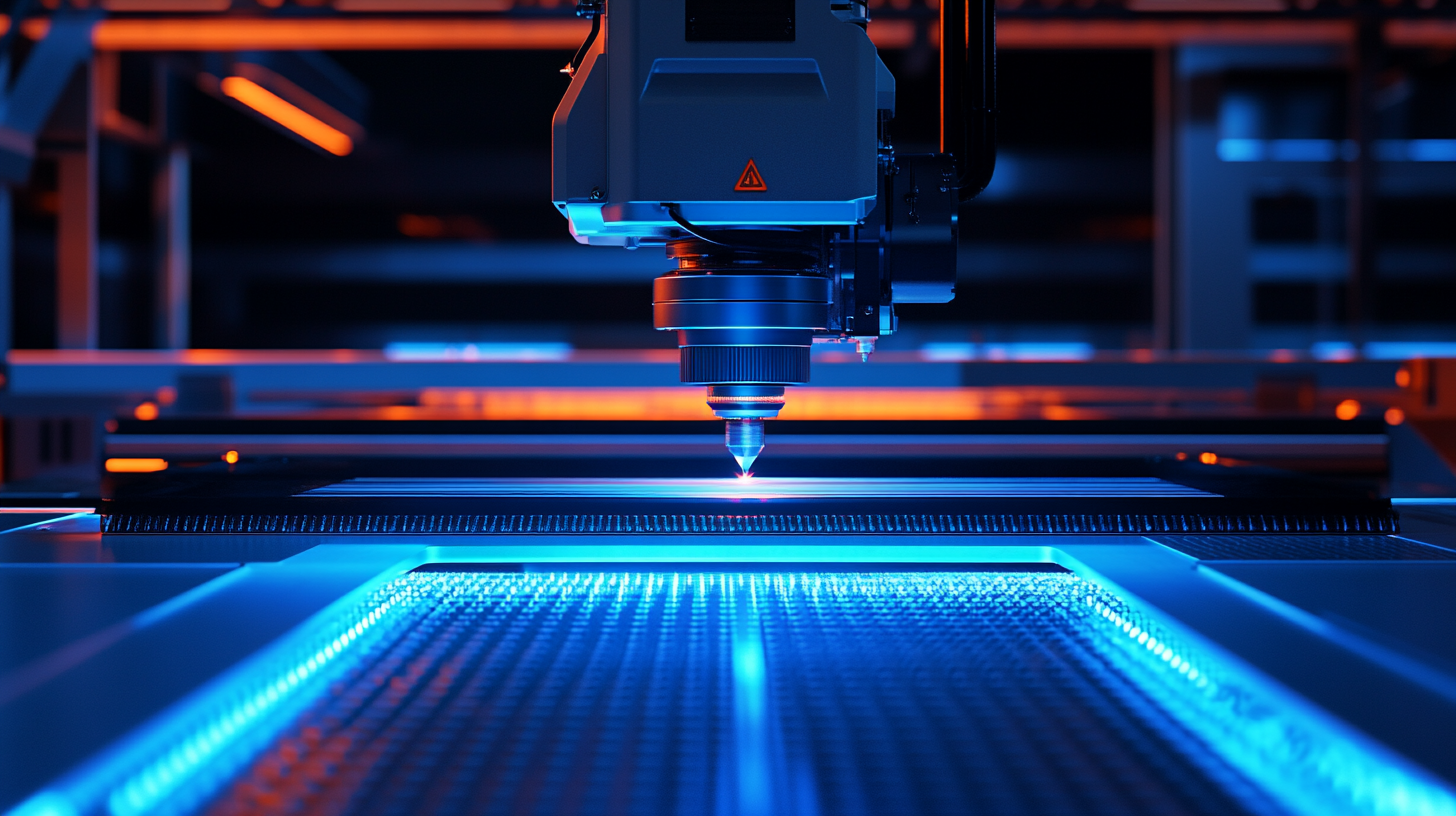
Emergence of Small Plasma Tables in the Manufacturing Landscape
In today’s evolving manufacturing landscape, the emergence of small plasma tables is making waves by transforming traditional metal fabrication processes. These compact cutting machines offer precision and versatility, enabling manufacturers to tackle intricate designs with ease. As capital expenditures (capex) in the metal fabrication industry are on the rise, nearly matching pre-pandemic levels, small plasma tables are becoming increasingly appealing for manufacturers looking to enhance their productivity without significant overhead costs. The resurgence in capex spending signifies a renewed confidence in the manufacturing sector, with companies investing in advanced technologies to streamline operations. Small plasma tables are particularly beneficial for small to medium-sized businesses that require high-quality cutting solutions in a compact footprint. By adopting these tools, manufacturers can reduce waste, increase efficiency, and respond more swiftly to market demands, ultimately gaining a competitive edge. Additionally, the rise of small plasma tables reflects the broader trend toward customization in manufacturing. As customer preferences shift towards bespoke solutions, the agility offered by these tables allows for rapid prototyping and tailored production runs. This adaptability not only meets the unique needs of clients but also paves the way for innovation in product development. As more manufacturers recognize the advantages of integrating small plasma tables into their operations, the future of precision cutting looks brighter than ever.
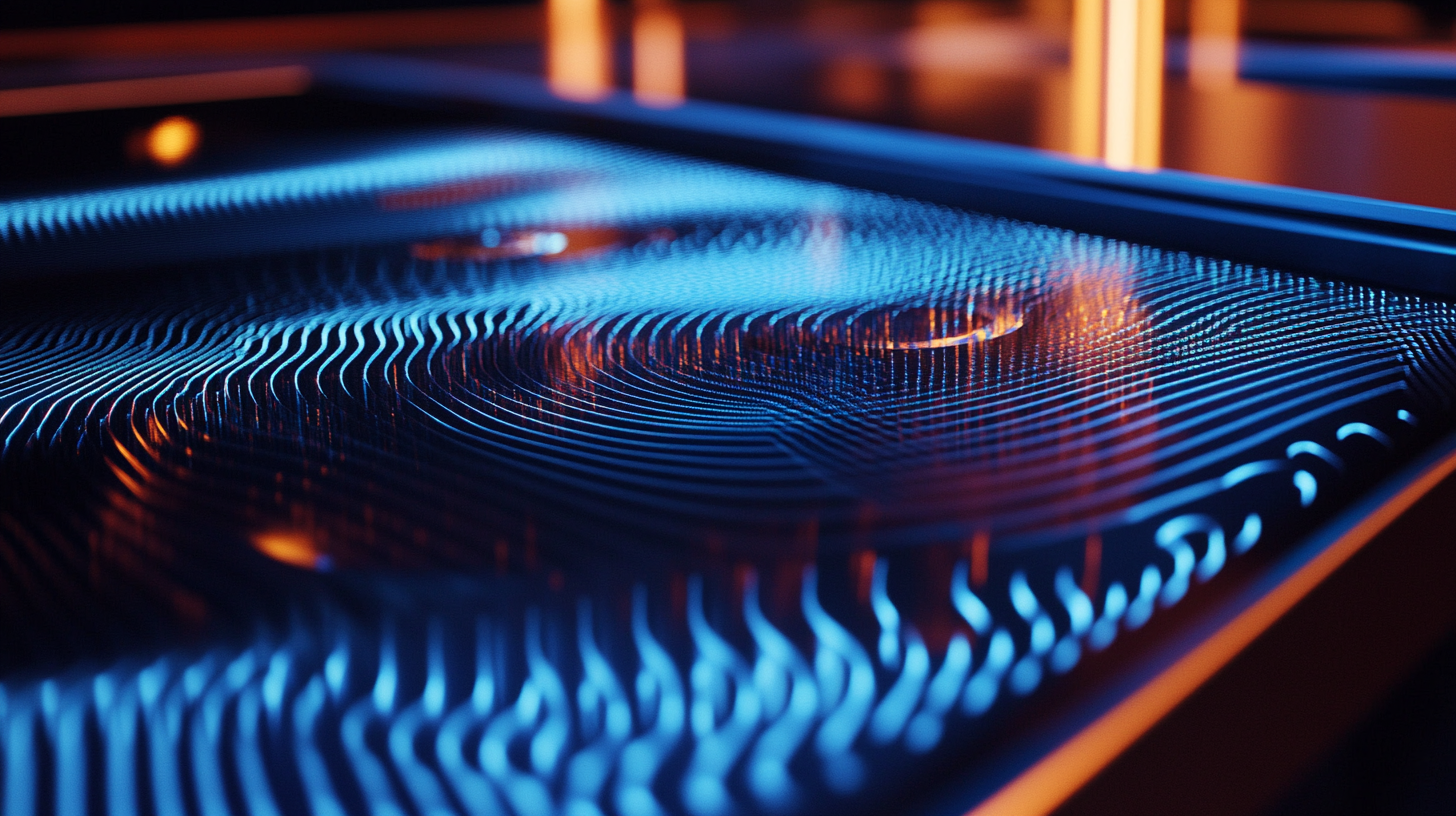
Key Advantages of Precision Cutting for Global Manufacturers
The landscape of global manufacturing is continually evolving, and precision cutting has emerged as a pivotal technology in this transformation. Small plasma tables are at the forefront, offering manufacturers enhanced accuracy and efficiency in their cutting processes. These compact machines are designed for versatility, allowing users to easily adapt to various materials and shapes with minimal downtime.
One of the key advantages of precision cutting lies in its ability to reduce waste significantly. Traditional cutting methods often lead to material overuse and excess scrap, increasing costs and environmental impact. With small plasma tables, manufacturers can achieve tighter tolerances and more efficient layouts, ensuring that every cut counts and resources are utilized to their fullest extent.
Moreover, the speed of operation provided by plasma cutting technology cannot be understated. In a fast-paced manufacturing environment, the ability to quickly produce high-quality components gives companies a competitive edge. Smaller plasma tables allow for rapid setup and execution, enabling manufacturers to respond promptly to market demands without sacrificing precision. This agility in production not only boosts productivity but also improves overall customer satisfaction, as order fulfillment times shrink, and quality remains high.
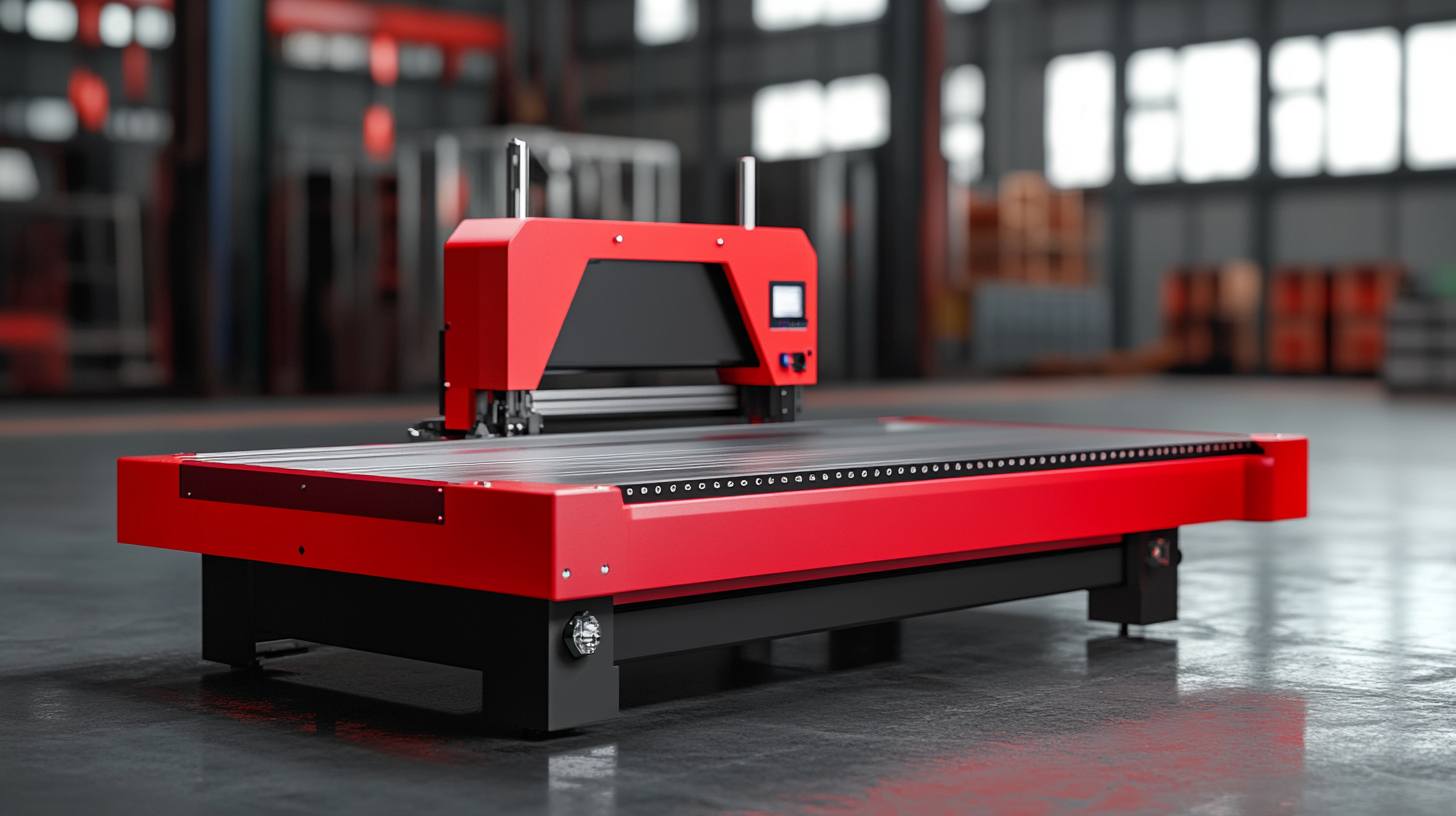
How Small Plasma Tables Enhance Production Efficiency
In the fast-evolving landscape of manufacturing, small plasma tables are making significant strides in production efficiency. According to a report by MarketsandMarkets, the global plasma cutting equipment market is projected to reach $7.8 billion by 2026, highlighting the increasing adoption of advanced cutting technologies across various industries. Small plasma tables, in particular, are gaining traction among manufacturers looking to optimize their workflows while maintaining precision and quality.
One of the key advantages of small plasma tables is their ability to perform intricate cuts with minimal material waste. A study by the Fabricators & Manufacturers Association International indicates that manufacturers can reduce material costs by as much as 15% when using precision cutting technologies. This efficiency extends to time savings as well; small plasma tables are known to operate at speeds up to 50 inches per minute, significantly decreasing production cycles compared to traditional cutting methods.
Furthermore, small plasma tables are designed to integrate seamlessly with modern manufacturing processes, including automation and CNC technology. This integration allows manufacturers to implement just-in-time production strategies, which can lead to improved inventory management and reduced lead times. As businesses continue to seek ways to enhance their operations, the shift towards small plasma tables is becoming a game-changing factor in achieving both efficiency and competitive advantage in the global market.
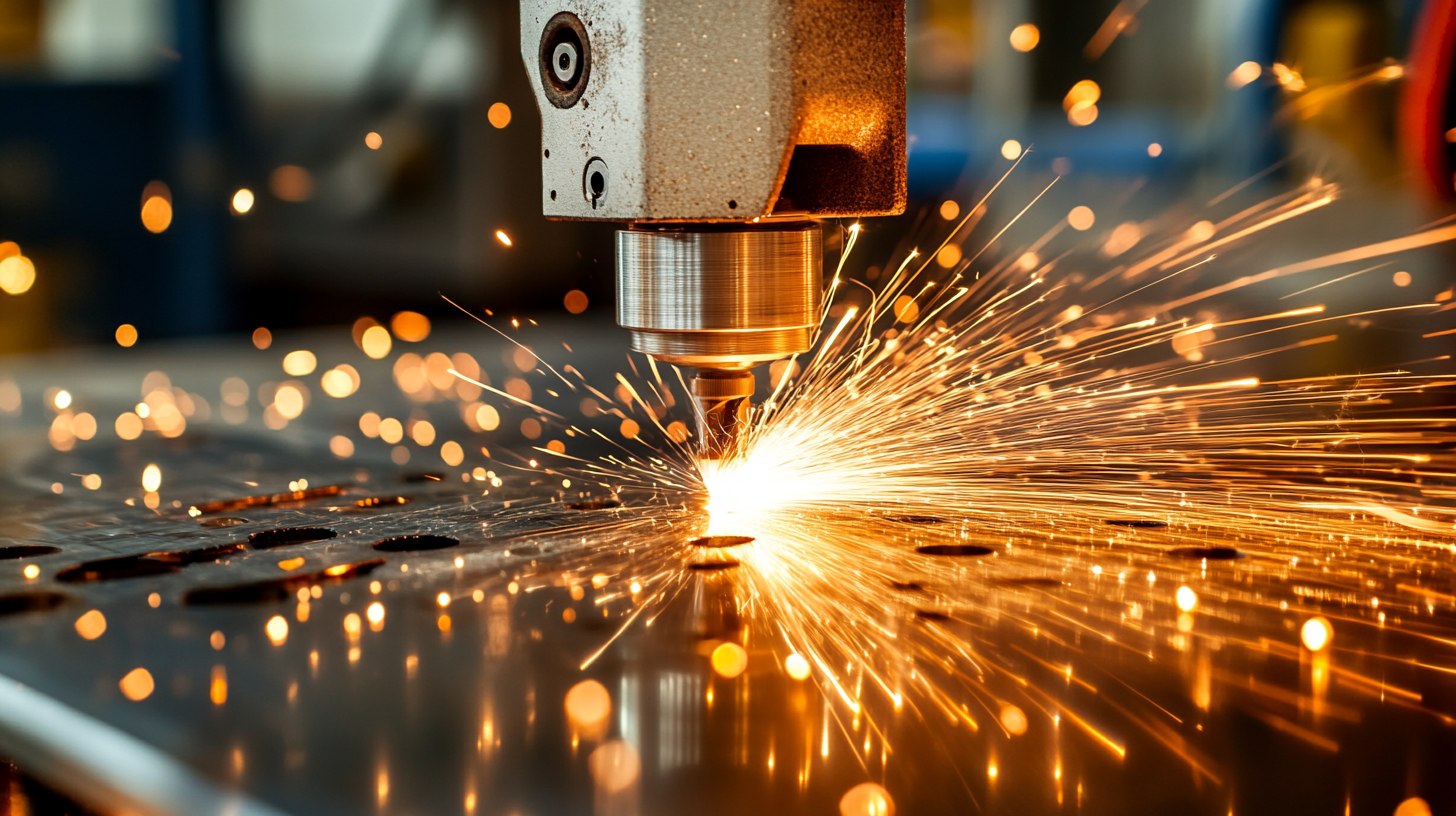
Innovative Applications of Plasma Cutting Techniques
The advancements in plasma cutting technology have opened up a multitude of innovative applications, particularly for small plasma tables tailored for global manufacturers. As industries strive for efficiency and precision, plasma cutting has emerged as a favored technique due to its versatility and cost-effectiveness. According to a report from MarketsandMarkets, the global plasma cutting machines market is projected to reach USD 8.02 billion by 2025, growing at a compounded annual growth rate (CAGR) of 5.2% from 2020. This growth is reflective of the increasing demand for high-quality cuts in a variety of materials, including metals, plastics, and composites.
Small plasma tables are particularly beneficial for manufacturers looking to optimize their production processes. Their compact size allows for greater flexibility in workshop layouts, enabling companies to maximize their workspace without compromising on efficiency. Industries such as automotive, aerospace, and fabrication are utilizing these machines to produce intricate components with minimal waste. A study from the Fabricators & Manufacturers Association highlights that plasma cutting can achieve a cut speed that is up to five times faster than traditional methods, thereby reducing operational downtime and enhancing overall productivity.
Furthermore, the precision offered by modern plasma tables has been a game-changer in design and prototyping. Manufacturers can now execute complex designs that were previously unattainable, thanks to advanced software integrations that streamline the cutting process. This technological synergy enables quicker turnarounds and fosters innovation within product development cycles. A survey conducted by the National Institute of Standards and Technology indicates that 60% of manufacturers report significant improvements in product quality through the adoption of advanced plasma cutting techniques, underscoring the transformative power of this technology in the manufacturing landscape.
Future Trends in Plasma Cutting Technology for Manufacturers
The landscape of plasma cutting technology is evolving rapidly, with small plasma tables taking center stage for global manufacturers. As industry demands shift toward precision and efficiency, manufacturers are turning to innovative solutions that promise greater performance. According to a recent report from MarketsandMarkets, the global plasma cutting market is projected to reach $4 billion by 2027, growing at a CAGR of 8.1% from 2022 to 2027. This growth is driven by the increasing demand for precision cutting across various sectors, including automotive, aerospace, and metal fabrication.
Future trends in plasma cutting technology indicate a significant emphasis on automation and integration. With advancements in software and machine learning, manufacturers can expect enhanced capabilities like real-time monitoring and predictive maintenance. The 2022 Industrial Robotics Report highlights that nearly 40% of manufacturers are expected to integrate automated solutions into their cutting processes by 2025, highlighting a shift towards more autonomous operations. Small plasma tables equipped with these technologies will enable companies to reduce downtime and improve overall production efficiency.
Additionally, the advent of eco-friendly cutting techniques is gaining traction. The International Journal of Advanced Manufacturing Technology suggests that sustainable practices may dominate the market by 2028, with manufacturers seeking options that minimize waste and energy consumption. Innovations such as high-efficiency plasma torches and advanced materials are emerging, allowing manufacturers to adopt greener practices without compromising cutting quality. This focus on sustainability not only meets regulatory standards but also aligns with consumer expectations for environmentally responsible manufacturing.