Understanding Industry Standards: What Sets the Best Plate Laser Cutting Machines Apart?
In the rapidly evolving world of manufacturing, understanding the intricacies of industry standards is crucial, especially when it comes to selecting the best Plate Laser Cutting Machines. As these machines become indispensable tools for enhancing precision and efficiency in various applications, it's essential to distinguish the top-tier options from the rest. This blog delves into the critical factors that set exceptional Plate Laser Cutting Machines apart, focusing not only on their technical specifications but also on the often-overlooked aspects of after-sales service advantages and maintenance costs.
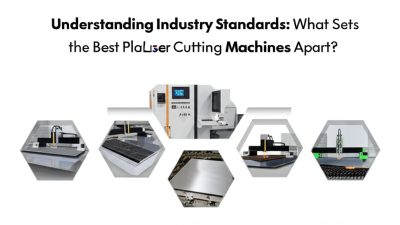
With digital insights and practical tips, we aim to equip manufacturers with the knowledge needed to make informed decisions, ensuring that they choose a laser cutting machine that not only meets their operational needs but also provides long-term value.
Key Features of High-Performance Plate Laser Cutting Machines
When it comes to selecting a high-performance plate laser cutting machine, certain key features distinguish the best models from the rest. One of the most critical aspects is the machine's precision and cutting speed. High-quality laser cutting machines are designed to deliver exceptional accuracy, allowing for intricate designs and tight tolerances without compromising the cutting speed. This combination of precision and efficiency is vital for industries that require both quality and rapid production.
Another essential feature is the versatility of the cutting machine. Top-tier models often come equipped with advanced software and technologies that allow for easy adjustments to different materials and thicknesses. This flexibility not only enhances productivity but also broadens the range of applications, enabling businesses to tackle various projects without needing multiple machines. Furthermore, user-friendly interfaces and automation technologies are increasingly becoming standard, making it easier for operators to achieve optimal results with minimal training.
Comparative Analysis of Industry Standards and Innovations
When assessing the best plate laser cutting machines, it’s essential to consider both industry standards and the latest innovations that differentiate leading products. Industry standards typically include factors such as cutting speed, precision, repetition accuracy, and overall energy efficiency. Machines that meet or exceed these benchmarks are often recognized for their reliability and performance in high-demand settings. However, as technology evolves, new features such as advanced software integration, automation capabilities, and user-friendly interfaces are becoming equally significant.
Innovations in laser cutting technology are further elevating industry standards. For example, some machines now utilize artificial intelligence to optimize cutting paths, significantly reducing waste and improving operational efficiency. Others incorporate enhanced cooling systems and modular designs to facilitate easier maintenance and upgrades. By staying attuned to these developments, businesses can not only comply with existing industry standards but also gain a competitive edge, ensuring their operations remain at the forefront of the manufacturing landscape.
The Importance of Precision and Speed in Laser Cutting Technology
In the world of laser cutting technology, precision and speed are paramount for achieving optimal results. The best plate laser cutting machines utilize advanced algorithms and high-performance components to deliver unmatched accuracy. Precision in laser cutting is measured in microns, which means that even the smallest discrepancies can lead to significant errors in the final product. High-quality machines employ state-of-the-art focusing optics and intelligent motion control systems that ensure each cut is executed flawlessly, reducing the need for costly rework.
Speed, on the other hand, directly impacts productivity and efficiency in manufacturing processes. Modern plate laser cutting machines are designed to operate at high speeds without sacrificing quality. This balance is achieved through features such as rapid accelerations, high-power lasers, and optimized cutting paths. As industries strive to meet increasing demand, the ability to process materials quickly while maintaining precision sets the best machines apart from their competitors. Ultimately, investing in equipment that excels in both precision and speed is crucial for businesses aiming to enhance their operational capabilities and stay ahead in a competitive marketplace.
Evaluating Material Compatibility for Optimal Laser Cutting Results
When it comes to laser cutting, material compatibility is key to achieving optimal results. Different materials—be it metals, plastics, or composites—react uniquely to laser energy. According to a report by the International Laser Cutting Industry Association (ILCIA), understanding these interactions can significantly enhance precision and efficiency. For instance, carbon steel can absorb laser energy effectively, which allows for a cleaner cut, whereas reflective materials like aluminum require specialized settings to avoid complications during the cutting process.
Moreover, the choice of laser type and power can be pivotal. A recent study published in the Journal of Manufacturing Processes highlighted that CO2 lasers are ideal for non-metal materials, providing a smoother finish compared to fiber lasers. Conversely, fiber lasers demonstrate superior speed and accuracy when cutting metals. Transitioning between materials not only demands a thorough knowledge of their thermal properties but also an in-depth understanding of the laser machine’s capabilities. This ensures that manufacturers can meet the diverse needs of their clients, maintaining high standards in production while maximizing efficiency.
Future Trends: What to Expect from Next-Gen Plate Laser Cutters
The landscape of plate laser cutting technology is evolving rapidly, driven by advancements in both materials and machine capabilities. Future trends indicate a shift towards more intelligent and automated systems that not only enhance cutting precision but also improve operational efficiency. Next-generation plate laser cutters will likely feature integrated artificial intelligence to optimize cutting paths and reduce waste, resulting in cost-effective production processes. These innovations promise to minimize human intervention while maximizing output quality.
Furthermore, future machines will focus on versatility, accommodating a broader range of materials and thicknesses with unmatched speed and accuracy. As industries adopt more sophisticated manufacturing processes, the demand for multi-functional laser cutting systems will rise. The integration of advanced sensor technologies will facilitate real-time monitoring, enabling operators to make informed adjustments on the fly. This heightened adaptability will be crucial for manufacturers looking to remain competitive in an ever-changing market. Overall, the next generation of plate laser cutting machines is set to redefine efficiency and precision, paving the way for a new era in manufacturing.